The Denver Regional Transportation District (RTD) services a 2,342 square mile service area covering eight counties in the Denver Metro Area. The agency offers bus, light rail and commuter rail services to 2.92 million riders annually. RTD’s focus is outlined in the agency’s Quality of Life (QoL) Study which aims to balance transit needs with regional growth, increase transit mode share, and improve transportation choices.
Denver RTD Boosts Data Accuracy with Object Maintenance Information Tool
172
light rail vehicles
49
SD 100s
123
SD 160s
Solving on-board problems
Testing
Better Data from System Maintenance
Conclusion
Contact
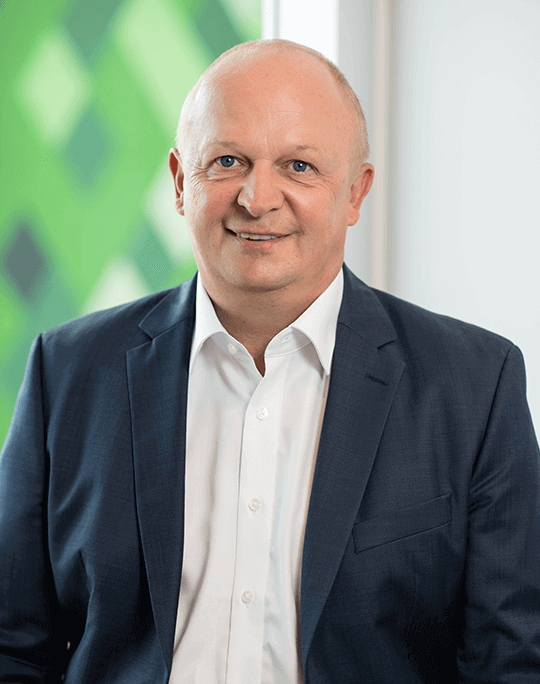
Andreas Rakebrandt
Business Development Director
INIT Inc
Virginia/USA